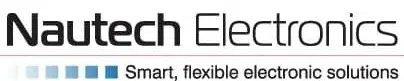
Nautech Electronics explain how AspectPL has given them real time metrics and OEE monitoring
In business for more than 30 years, Nautech operates a high-tech, automated factory in East Tamaki, Auckland. Nautech manufactures electronic circuit boards for many international companies and sectors such as automotive, marine, emergency services, aviation and military.
Nautech offers automated multiple SMT lines, automated optical and X-ray inspection, selective soldering machines, automated testing and a range of assembly robots.
“We manufacture hi-tech and high value electronic products and electro-mechanical assemblies, with a zero-defect policy. Every board has an ID barcode and AspectPL tracks every board through the process, monitoring throughput, defects and efficiency in real time.
Before we implemented AspectPL we had manual tracking processes in place like charts and spreadsheets. The problem was that we could only easily refer to non-current information – last month’s data. Now with AspectPL we have real time metrics and OEE monitoring.“
Andrew Turner, Managing Director, Nautech Electronics, NZ
How has the maintenance module helped you manage machine maintenance at your plant?
“Now all our machines (even non-monitored) and our maintenance team are set up in AspectPL. When a maintenance task is due it automatically sends an email to the correct maintenance team member to let them know that work needs to be done.
Automating machine maintenance has saved me a lot of time – no more reviewing spreadsheets. It almost self manages. AspectPL generates an action and informs the staff member who needs to perform it.”
Another advantage was that in the Cromford Pipe factory different machines work a lot harder than others. Some machines never stop, some machines work 2 weeks out of the month. This created a real imbalance in service schedules. Previously, machines that work a lot were prone to getting under serviced and the machines that didn’t work so hard were getting over serviced. Now they can track off the machine cycle times and see exactly how much a machine has worked and can design a maintenance schedule accordingly.
Luke says “Being able to track maintenance requirements off actual machine cycles is both a time-saving and cost benefit to us. I think in the future the data extract available from the maintenance module will also help us identify machine upgrades and capital purchases.”
It’s been 18 months since you implemented AspectPL - what advantages have you seen in that time?
“Implementing AspectPL MES software has been an absolutely huge positive change for our business. Previously calculating OEE was a significant task. It took a week and a half to download and analyse a month’s production – now with AspectPL it takes 20 seconds. Because analysing OEE was so difficult, it wasn’t one of our focusses – we operated about 50% which was very poor. Now it’s easy to calculate, we constantly review it and our OEE is between 70 and 80%. This means we are supplying more product; production is on time and our labour costs have reduced.
Previously we employed a production scheduler and production supervisor. As those people have left the business, we haven’t replaced them.”
Does the Cromford Pipe team like working with AspectPL?
“After the initial transition from paper to tablets our team really like it. Previously they were running around with clipboards losing paper everywhere, now they just add a metric or tick a box on their tablet. Tracking work orders has gone from a shuffling through a pile of paper to everything available on their screen.
AspectPL definitely revolutionised production for us. It has helped us through the current Covid-19 environment where unfortunately businesses need to run very lean.
We are very happy with the support we get from the AspectPT team. The guys are readily available and they are always really helpful and friendly.”