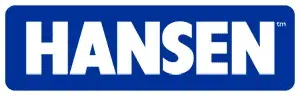
See how Hansen Products managed the AspectPL installation and how they are utilising data from the MES to improve their business."
A family owned company, Hansen Products have been making fittings and valves since the 1950s. Based in Whangarei, Hansen Products originally made brass fittings for the agricultural industry in New Zealand (NZ).
Known for high quality products with great tolerances, Hansen Products continues to make technically advanced plastic fittings and valves for the NZ and international markets. They believe in ‘Best Installed Value’ and achieve this with in-house R & D, product design, toolmakers, manufacturing, assembly, marketing, sales and distribution.
In 2018 Hansen Products saw there was a gap in their production data and decided to install AspectPL to digitise their production floor. Jon Kirby and Ian Kleingeld from Hansen Products explain how they managed the installation process.
How did you persuade Hansen Products management team that implementing AspectPL would benefit production?
Jon Kirby, Hansen Products Manufacturing Manager explains.
“We were aware of the benefits that AspectPL would provide from our research and site visits. We realised that we also wanted to have the team ready to take advantage of the information AspectPL made available – along with the benefits of the scheduling function.
To help with this decision the team implemented two of the benefits of AspectPL manually:
- The team started recording machine alarms. After 3 months, this information helped us to determine exactly when our screw tips needed replacing so we could do preventative rather than reactive maintenance.
- We changed our manual production board to represent the digital version on AspectPL. This immediately showed us constraints to achieving our plan. For example, we had 5 scheduled changes on the plan but only had 3 setters on at that time.”
How did you encourage buy in from the production floor staff?
Ian Kleingeld, Hansen Products Production Planner explains.
“To prepare the team we started collecting data at the machines a few months before the AspectPL install date. This instilled a discipline of using data and it also achieved a data framework. This meant going from paper based data to tablets wasn’t too much of a change for them.
Changing our manual production board to match the AspectPL TV screen before the install date also helped the team get used to the layout.”
Jon Kirby adds. “We went live on October 1st so we said September is our ‘get used to it’ month – we needed to get into good habits to facilitate this change. We had great buy in from the setters and by the time we got to October 1st we asked the question – “are we ready to go live?” and the answer from the production team was yes.”
Did the install process happen quicker than you had planned?
Ian says. “Yes, our install was a lot quicker than we planned. I had all the machines showing on the schedule in the first week. I really enjoy this kind of thing and it was an easy change because it added value. There was no resistance from me and certainly the guys in the production office had really good buy in – we weren’t dragging guys kicking and screaming to adopt it – they were into it.
Once AspectPL was live we took baby steps. We said we will only worry about anything greater than 5 minutes of downtime and we won’t worry about rejects just yet. We got used to downtime and then we added rejects and carried on like that. Now 6 months down the track we are decreasing the downtime parameters so we are slowly getting better and better. We didn’t go in there and say this is the new system – good luck!”
Bob Dedekind, AspectPT’s Technical Manager adds.
“Hansen Products handled the training and change management process very well. They took time to implement change. Their team was ready and very keen to start working with AspectPL and they were a pleasure to work with.”
It’s been 6 months since installation – Ian, how are you finding working with AspectPL now?
“The day to day is good – really enjoying it. The planning and scheduling is great and it is easy to make changes and know what jobs are coming up.”
What is the biggest improvement AspectPL has made for you at Hansen Products?
“The live planning, ability to make changes on the go and seeing the production changes flow through straight away. In our old system, we just had pieces of paper – that was the plan. You only had a rough idea of when jobs would happen and now with it going live you can see it on the board and know when jobs are actually going to run. You can plan better in terms of people and production flow. It’s a lot better than what we used to have.”
Was it difficult to learn how to use AspectPL?
“A little bit of a learning curve at initial set up. Trying to set up family tools and working out production rules but Bob from AspectPT was there to help us and I enjoyed playing with the software. The beauty is it’s all changeable.”
What other benefits has Hansen Products seen?
One of the unforeseen benefits was when Hansen Products did a raw material stocktake. There were massive variances and the AspectPL data revealed they weren’t taking into account the start up rejects and would only count actual production. With AspectPL Hansen Products are now able to take into account the start up rejects and their raw material stocktake is much more accurate.
Jon Kirby explains other benefits.
“The biggest benefit is that AspectPL has increased the transparency of our manufacturing processes. Because of this, we are learning about the constraints of our current manufacturing processes. Once you understand your constraints you can find ways to solve, eliminate or plan around them. What we have learnt about our constraints by putting in AspectPL has been beneficial.
Once we had the AspectPL data it became clear there was a lot of general knowledge amongst the setters that was not known or shared with the planning team. For example, we identified some tools that if set it up a certain way it could take 2 hours longer than the prescribed set up time. Because AspectPL made this anomaly visible we were able to ask the question – “Why does this take 2 hours longer than the prescribed set up time?” AspectPL helped us identify constraints like this and we have been able to plan according to our constraints.
AspectPL has also given the setters a greater understanding of what we require – it’s visual, there is nowhere to hide. Now our setters know what tool change they have to do in what order for us to achieve the plan.”
Another anomaly AspectPL revealed was the plan was not taking into account that a setter needs 30 minutes post tool change to complete admin and do machine checks. Now these 30 minutes blocks are scheduled into the plan. Hansen Products even uses AspectPL to schedule product trials and machine maintenance into production.
Did you ask for any special requests from AspectPT?
Jon says “I have never been told ‘no’ from AspectPT – even when we asked for customisation.”
Hansen Products have installed Netstal machines which can run unattended. These machines set a challenge for AspectPL. Because the machines can run unattended that means some jobs are started during work hours and run into the night. When the job is finished at night Hansen Products can’t start a new job because their setters are tucked up in bed at home. This means when jobs stop at night AspectPL has to push the next job into the ‘manned’ window when the die setters return the next morning.
Bob Dedekind from AspectPT explains.
“The ability to push jobs into a manned window was a very sensible suggestion from Ian. So much so we have implemented this feature into AspectPL and rolled this out to all our clients.”
"The single most important thing is the transparency that AspectPL affords our manufacturing processes and team."
Jon adds “Accessing the data in the factory and the planning office is fantastic. The single most important thing is the transparency that AspectPL affords our manufacturing processes and the team. We are now able to plan what we are physically able to do. Before the plan was theoretical.”