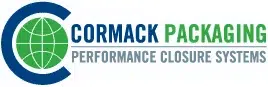
Cormack Packaging tell us about how AspectPL saved them days of work by streamlining production planning.
About Cormack Packaging
Established in Sydney in the 1940s, Cormack Packaging is an Australian family owned business, spanning three generations. Cormack celebrated its 80th birthday in 2019. Cormack’s head office and manufacturing plants are Sydney based and they also have offices in Melbourne and Auckland, New Zealand.
Cormack Packaging has a long history of working with leading consumer brands. They manufacture and import bespoke closure systems for a wide range of customers. Markets include insect and pest control, chemical and cleaning, garden, lawn and pet care, pharmaceutical health and wellbeing, automotive and hardware, food and beverage.
Predominately a 24/7 operation, Cormack runs 51 work centres across 3 sites with injection moulding machines from 50T to 400T, plus purpose built assembly lines.
In August 2018 Cormack Packaging installed AspectPL in their Sydney plant. Shaun Wallace and Jennine Newey tell us about their experience.
"AspectPL has made a huge difference. The biggest impact is in planning and scheduling."
Shaun Wallace, Cormack Packaging’s Production Manager explains.
“Previously our planning information wasn’t totally accurate – there was an element of guesswork involved. We’d count boxes off the machine. The machine makes the product, we pack boxes, we count the number of boxes made. With AspectPL we have full visibility and real time reporting on what’s actually happening.
Previously we did our planning in Axapta (MS AX). Axapta is an ERP system that can plan but has zero shop floor control and zero scheduling ability. After we created a plan in Axapta we would then export the plan to an access database to schedule which machines are running what jobs, in what order. Then we would create a separate spreadsheet with a gant chart to highlight the scheduling gaps. When we finalized all that we would print out a report which told us what dates we had to update back into Axapta so we knew when to buy the materials for the scheduled jobs. That took 3 solid days.
Inevitably in production things change, machines break down, customers have urgent requests. Our production plan was complex, paper based and very dynamic with frequent changes. Because we work 24 hours a day you could come in the morning and find that we followed the original plan even though it may have previously been changed.”
"AspectPL is a visual planning system and for a planner’s mind it fits beautifully."
“The previous system was cumbersome and it took too long to get a planner up to speed. The good thing about AspectPL is that it is user friendly, it’s a visual planning system and for a planner’s mind it fits beautifully.”
Shaun adds. “As soon as we installed AspectPL we scrapped the paper production plan completely. Every team member has a 10 inch tablet. The team just looks on their tablets for the next scheduled job – that’s it.
In the old system if you wanted to insert a job you had to re-run the entire plan again. That meant the full export, the full import, the full manual juggling and the full ERP update. Now we install the job, we put it in the plan and everything’s updated – it takes minutes rather than hours. The previous system was just too cumbersome. AspectPL allows flexibility we didn’t have before.”
How many days and hours are the production team saving because of AspectPL?
Jennine Newey, Cormack Packaging’s Production Planner explains.
“We wanted a seamless system. Export upload in and export upload out. Once a week I can sit and raise all the work orders in Axapta ERP, export them into AspectPL. The AspectPL scheduler is very easy to use – it’s very intuitive and takes little time to schedule. We schedule 250 work orders per month – previously this took 3 days to complete, now it takes only 1 day.
We save over 20 man hours per week on supervisors completing production reports. They used to spend 1.5 hours per shift, 3 times a day, 5 days per week – just on reports. They don’t have to think about it now – they just push a button and send it through – there’s the output for the day.”
Now planning time has been reduced by 2 days what do you spend the extra time doing?
Shaun says “Now I can work with the guys on the factory floor to optimize production. Currently we are working on making our changeovers faster, improving our line start and line clearance downtimes and reducing waste. With AspectPL we can see these stats at the push of a button – and in real time.”
How has AspectPL helped your technicians with production?
Jennine says. “There are 2 areas that are key to getting the machines ready for production – the tool room and the mould room. What’s important for the technicians is the mould number – not the product description. Chris Rauch at AspectPT helped us get our mould numbers printed on the production schedule. This means our technicians can see which job is scheduled next.
I use an analogy of the McDonalds drive through. The information is in one place and there is no guesswork. Everyone’s got a screen and everyone can see what is happening and if one person makes a change, the change is visible to everyone. You don’t have to spend your time constantly updating everyone – no one is waiting on an email.
We also worked with the AspectPT team to block out a time for preventative maintenance. This means we can schedule preventative maintenance without it affecting the actual production schedule.”
As Production Planner please tell us about your experience using AspectPL
Jennine says. “I love using AspectPL – it’s so easy to use and everything is visible. You can easily move jobs from machine to machine and look at ‘what if’ scenarios. When you’re talking to the die setters or the production supervisors you are all looking at the one screen, it’s not a sheet of paper. I think people are more engaged with the screen rather than having a sheet of paper.
It’s a great tool to visually see what is happening – our Customer Service team can see right down to the minute when a job is starting and when it’s running.
You also have the ability to track the plant remotely. For those of us who don’t sleep and wake up in the middle of the night, you can log on and see exactly what’s happening during the night shift.”
"AspectPL is definitely paying for itself."
Shaun adds. “We collect lots of data. We’ve had a database running since 2007. The export coming out of AspectPL is still propagating that same database. This means we’ve managed to maintain our reporting structure with no impact whatsoever.
One of the advantages of AspectPL is that it has the ability to grow with us. The AspectPT team listens to our feedback, requests for changes and improvements. As the AspectPT team develop updates and improvements they become part of the package for everyone. Other software vendors charge for individual updates – AspectPT does not.
AspectPL has provided us with an excellent shop floor control and planning system. We are getting a good return on our investment this will continue to improve as we become more familiar and skilled with the system.”