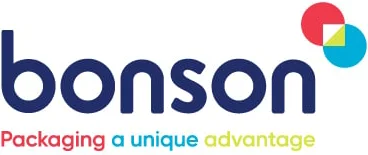
How Bonson uses AspectPL to keep ahead of the pack.”
Bonson is an Auckland based, family owned company that manufactures injection moulded rigid plastic food containers. Founded by brothers David Tsui and Johnny Chui in 1984, it employs about 60 staff. Bonson produces over a million units a day in one of Australasia’s most sophisticated and tightly run food grade manufacturing plants.
From day one, David and Johnny had big plans for the business. They’ve had to relocate to larger premises many times to cope with strong growth. Take a guided tour of their 24/7 factory and one of the first photos you’ll see is of David beaming proudly before a big red shipping container – the company’s first export to eagerly awaiting customers in Australia. Today, Bonson exports 60% of production to that market.
How has a New Zealand company in the ultra competitive packaging market achieved such success? By focusing relentlessly on quality and efficiency, says Production Engineer James Harper. “Most factories operate on the principle that everything that comes off the production line is good until proved otherwise. We take the opposite view. Until proved otherwise, everything is a reject.”
Designed for the plastics industry
Like most factory operations founded in the 80s, Bonson initially used manual systems for managing their production. But as David Tsui puts it: “We reached a point some years ago where, if we wanted to grow further, we needed to embrace technology and digitise our factory environment. We recognised that using clipboards and manually recorded production data were things of the past and we need to change. The best technology we’ve found is AspectPL.”
AspectPL is machine connected, manufacturing productivity software for discrete manufacturers such as those in the plastics injection and blow moulding industries. Bonson use many of AspectPL’s functional components including Planning and Scheduling, Monitoring, Production Scanning and Root Cause Analysis. These provide factory managers with unprecedented visibility and control over every aspect of daily operation.
“Equally important, AspectPL allows us to set a benchmark for quality. With AspectPL’s traceability function, if we produce a faulty product, we can go right back and see what machine produced it, what time it was made, who packed the box it was in, and how the machine was operating for hours either side of the product’s manufacture. “When you can do all that, you have all the say over the quality of your products.”
“My advice – if you want to grow, adopt this technology.”
“AspectPL helps us manage growth,” says David. “It means less manpower, more accuracy, real time tracking and fantastic control of the whole production process. It’s allowed us to scale the business without scaling our data collection or factory management approach.”
What’s more, because AspectPL connects to the accounting system, yield from the factory is automatically updated into stock.
With AspectPL gross utilisation of the manufacturing equipment increased from 70% to 95% and above, virtually eliminating unplanned downtime and manufacturing overruns on any of the machines. “My advice to any company committed to growth is to adopt this technology. But you’ve also got to be prepared to change how you do things and act on the insights it provides on how your factory is operating. Management has to buy fully into it. Here at Bonson, the management and the board are interested in the information provided by AspectPL and use it to make important decisions on a daily basis.”
In fact, he adds, everyone has to be involved. One of the biggest changes for Bonson has been putting the technology into the hands of its factory floor personnel, each of whom carries a mobile, wireless scanner to record activity at their machine and to scan the finished products. That change is more than functional; it’s also given staff a personal stake in production quality. The biggest pitfall, says David and James, is to adopt an “all is rosy” mentality. AspectPL is designed to highlight where the opportunities for improvement are – and that means drawing attention to current inefficiencies. “It’ll show you things you don’t want to see, even when you’re operating really well,” says David.
“Now that we’ve achieved the scale we were after, we’re putting more focus on further incremental improvements in quality and greater responsiveness to customer requests. This is a great position to be in – to know we’re setting an industry benchmark, and yet, thanks to the technology at our disposal, we’re still able to take new ground.”
World class plastic food packaging production facility with food grade hygiene standards.
High quality, safe packaging is a must when it comes to manufacturing plastic containers and packaging for the food industry. Bonson 6000 m2 state of the art production facility was purpose built with this in mind and is filled with the latest plastic injection, robotic and in-mould labelling (IML) technology operating 24/7.
The facility adds multiple layers of dependability to the production process through stringent quality, food hygiene and health and safety systems which are maintained through independent ISO 9001, AS/NZS 4801 and HACCP certification.