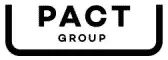
Lance Wyatt from PACT Packaging in Hamilton explains how AspectPL MES is helping him manage this high volume, low margin food packaging operation.
Operations Manager Lance Wyatt has been at Pact Packaging Hamilton (previously known as Alto) for 37 years and is described as someone who knows how to get stuff done. Twelve months ago, he did just that by implementing the AspectPL manufacturing execution system software (MES) at Pact Packaging in Hamilton. Lance took charge of the project and deserves much of the credit for leading a successful implementation.
About Pact Packaging Hamilton
AspectPL MES was implemented in the Hamilton Food Packaging business due to the high-volume nature of the operation.
Lance says. “This high volume, low margin business needs every advantage it can get. The team is focused on quick turnaround projects to improve productivity and AspectPL helps analyse the plant’s downtime and product issues.”
The food packaging business has 70 operational staff and multiple varied machines. Pact’s food packaging plant through-put is significant. They run high speed multi-cavity machines including the capacity to print.
This plant mostly makes packaging for products in the supermarket chiller aisle including yoghurt and butter tubs and icecream and dip containers.
Why invest in a manufacturing execution system software (MES) like AspectPL?
“I knew about AspectPL because we had used it very successfully at our Mount Wellington site in Auckland.
We implemented AspectPL because there was a large gap between our operational manufacturing processes and our ERP data system – SAP. All SAP sees is the pallet when the product is finished. We didn’t actually know what our downtime was and the reasons for the downtime – with AspectPL we can see detail down to each individual machine cycle. I also wanted software that could record our quality information which links directly to the product that has been made.
AspectPL gives us clarity – we can see everything now – OEE live, the schedule and downtime as it occurs. Previously we used whiteboards to manage our lean manufacturing programme and now we use the AspectPL digital screens – it was definitely the next logical step to increase our productivity.”
AspectPL MES Implementation process
The Hamilton plants’ small implementation team included Lance, a process technician and 2 electricians. The PACT IT team managed the server requirements and the electrical team managed the cabling.
Lance explains. “AspectPT helped design the PLC loop and relays. The IT solution from AspectPL was excellent, the platform is very stable and works really well.
The implementation part was quite easy. After the cabling was completed, it took about 3 weeks to get up and running and we were well supported by AspectPT.
Our production team were excited to get into it – they are very flexible, open to change and keen to try new things.”
Twelve month AspectPL MES report card
So, 12 months on how is AspectPL performing?
“The visibility of knowing what is running when and how well it is running in the plant is great. You can walk into the production office and see exactly what is happening – what machine is up, what is down. Because our site is very large, operators can see on their tablets what is happening at machines 100 meters apart and they can also read other shifts comments in AspectPL. If there is a product problem we can go back and analyse the machine cycle time and start up rejects. Downtime information also helps us make improvements.
We are definitely seeing a return on investment in dollars, time and machine productivity. It’s very difficult to operate a plant effectively without AspectPL – there is no focus on outputs. With AspectPL you know that your outputs are right so you don’t need to worry so much about your inputs. You can minimise downtimes, check cycle times and running rejects.”
What is next for AspectPL MES at Hamilton?
Lance says. “In time I would like to use AspectPL a lot more comprehensively. I believe AspectPL can become a significant management tool for the team by using data like tallys and action messages in operational meetings to define priorities.”